Ultrasonic cleaning process, solution and distribution of transducers in the cleaning tank
Browse Volume:1457 Classify:Support
Ultrasonic cleaning process and selection of cleaning solution
Before purchasing a cleaning system. The following application analysis should do on the cleane parts: Clarify the material composition, structure and quantity of the cleaned parts, analyze and clarify the dirt to be remove. These are all to decide what cleaning method to use and judge the application Aqueous cleaning solutions are also a prerequisite for the use of solvents. The final cleaning process needs to be verified by cleaning experiments. Only in this way can a suitable cleaning system, a rationally designed cleaning process and a cleaning solution be provided. Considering the influence of the physical properties of the cleaning fluid on ultrasonic cleaning. The vapor pressure, surface tension, viscosity and density should be the most significant influencing factors. Temperature can affect these factors, so it also affects the efficiency of cavitation. Any cleaning system must use cleaning fluid.
When choosing a cleaning fluid, three factors should consider
1. Cleaning Efficiency:
Be sure to experiment when choosing the most effective cleaning solvent. If ultrasound is introduced into the existing cleaning process, the solvent used generally does not need to be changed;
2. Simple operation:
The liquid used should be safe and non-toxic, easy to operate and have a long service life;
3.Cost:
The cheapest cleaning solvent is not necessarily the least expensive to use. In use, factors such as cleaning efficiency, safety, and the highest utilization rate of work pieces that can be cleane by a certain amount of solvent must be consider. Of course, the cleaning solvent chosen must achieve cleaning results and be compatible with the work piece material being cleaned. Water is the most common cleaning solution. So systems using water-based solutions are easy to operate, low in cost, and widely used. However, for some materials and soils, etc., it is not suitable for aqueous solutions, so there are many solvents available. Different cleaning fluids, different cleaning systems
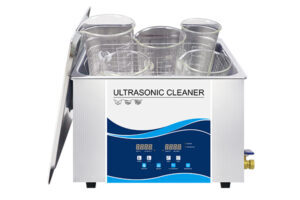
Lab equipment cleaning
Aqueous Systems:
Usually consisting of an open tank in which the workpiece is submerged. The complex system consists of multiple tanks and is equip with a circulating filter system, a shower tank, a drying tank and other accessories.
Solvent system:
Most of them are ultrasonic vapor-phase degreasing cleaning machines, often equipped with continuous waste liquid recovery devices. The ultrasonic vapor phase oil removal process is completed by an integrated multi-tank system consisting of a solvent evaporation tank and an ultrasonic dip tank. Oil, grease, wax, and other solvent-soluble soils are removed by the combined use of hot solvent vapor and ultrasonic agitation. The work piece unloaded after a series of cleaning processes is hot, clean and dry.
Cleaning parts processing
Another consideration for ultrasonic cleaning is the loading and unloading of the cleaning parts, or the design of the tooling in which the cleaning parts are place. When the cleaning piece is in the ultrasonic cleaning tank, neither the cleaning piece nor the cleaning piece basket shall touch the bottom of the tank. The total cross-sectional area of the cleaning parts should not exceed 70% of the cross-sectional area of the ultrasonic tank. Rubber and non-rigid plastics absorb ultrasonic energy, so caution should be exercise when using these materials in tooling. Insulated cleaning parts should also give special attention. Improperly designed tooling baskets, or holding work pieces that are too heavy. Can greatly reduce the efficiency of even the best ultrasonic cleaning systems. Hooks, racks and beakers can be use to support cleaning pieces.
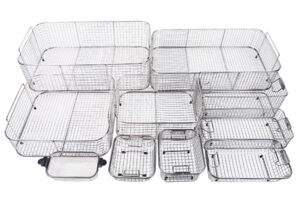
Granbosonic cleaning basket
Cleaning time: 3-10 minutes, preferably timing.
The distribution and bonding of transducers in the cleaning tank
At present, some ultrasonic cleaning machine products are too densely distribute with transducers stick to the bottom or wall of the cleaning tank, one next to the other. The electric power intensity of the input transducer reaches 2-3 watts per square centimeter. On the one hand, such high intensity will accelerate the cavitation corrosion of the surface of the stainless steel plate (the surface in contact with the cleaning liquid) and shorten the service life. On the other hand, due to the sound intensity too high. A large number of large bubbles will be generate near the surface of the steel plate. Which will increase the sound transmission loss and weaken the cleaning effect far from the transducer.
Generally, it is appropriate to choose the power intensity of less than 1.5 watts per square centimeter (calculated according to the area of the steel plate with the transducer attached). If the cleaning tank is deep, in addition to the transducer on the bottom of the tank, the transducer should also bond on the tank wall.
The bonding quality of the transducer and the cleaning tank has a great influence on the quality of the ultrasonic cleaning machine.
Not only must it firmly adhere, but also the adhesive layer should uniform, without lack of glue and no cracks, so that the ultrasonic energy can transfer to the cleaning solution to the maximum extent. In order to improve the efficiency of the whole machine and the cleaning effect. Some cleaning equipment is currently use to prevent the transducer from falling out of the cleaning tank. The fixing method of screws and glue is adopt. Although the transducer will not fall off in this connection method, there are many hidden dangers. If the welding quality of the screw is poor.
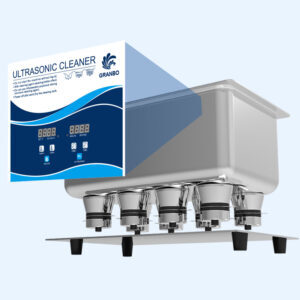
Transducer distribution
For example, it is not perpendicular to the surface of the stainless steel plate, the glue layer will uneven, and even there will be cracks or lack of glue, and the energy transmission will weaken; Cavitation corrosion, shorten the service life.
One of the ways to judge the quality of bonding is to measure the temperature rise of the transducer after the cleaning tank is fill with water and turn on for a period of time. If the temperature of a transducer among many transducers rises very fast. It means that the transducer may not bond well. Because the sound radiation is not good at this time. Most of the electrical energy is consume on the transducer and generates heat . Another method is to measure the electrical impedance of the transducers one by one under the condition of small signal to judge the bonding quality.
Hello!