Selection and cleaning process of ultrasonic cleaning machine
Browse Volume:1582 Classify:Support
1.The choice of power
The effect of ultrasonic cleaning is not necessarily proportional to (power x cleaning time), sometimes with low power, it takes a long time to remove the dirt. And if the power reaches a certain value, the dirt is sometimes quickly removed. If the selected power is too large, the cavitation strength will be greatly increased, and the cleaning effect will be improved, but at this time, the more precise parts will also be corroded, which is not worth the loss, and the cavitation at the vibration plate at the bottom of the cleaning tank will be serious, and the water point corrosion will also increase. When using organic solvents such as trichloroethylene, there is basically no problem, but when using water or water-soluble cleaning liquid, it is easy to be corroded by water pits. Therefore, the ultrasonic power should be selected according to the actual usage.
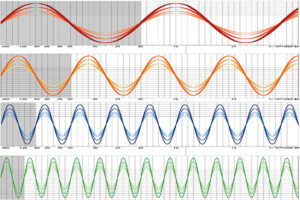
the choice of power and frequency
2.The choice of frequency
The frequency of ultrasonic cleaning is between 28kHz and 120kHz. The physical cleaning force caused by cavitation when using water or water cleaning agent is obviously beneficial to low frequency, generally around 28-40kHz. For cleaning parts with small gaps, slits and deep holes, it is better to use high frequency (generally above 40kHz), even hundreds of kHz. When cleaning watch parts, use 400kHz. If the broadband frequency modulation cleaning is used, the effect is better.
3. The use of cleaning baskets
When cleaning small parts, mesh baskets are often used. Since the mesh will cause ultrasonic attenuation, special
Don’t get noticed. When the frequency is 28khz, it is better to use a mesh of more than 10mm.
4.The choice of cleaning fluid temperature
The most suitable cleaning temperature of the water cleaning solution is 40-60°C, especially when the weather is cold, if the temperature of the cleaning solution is low, the cavitation effect is poor, and the cleaning effect is also poor. Therefore, some cleaning machines wind the heating wire outside the cleaning cylinder to control the temperature. When the temperature rises, cavitation is easy to occur, so the cleaning effect is better. When the temperature continues to rise, the gas pressure in the cavitation increases, causing the impact sound pressure to drop, reflecting the multiplication of these two factors.
5. Determination of the amount of cleaning fluid and the location of cleaning parts
Generally, it is better that the cleaning liquid level is 100mm or more higher than the surface of the vibrator. Because the single-frequency cleaning machine is affected by the standing wave field, the amplitude at the node is small, and the amplitude at the wave amplitude is large, resulting in uneven cleaning. Therefore, the best choice for cleaning items should be placed at the amplitude.
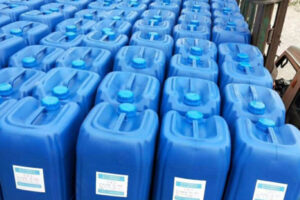
the cleaning solution
6. Ultrasonic cleaning process and selection of cleaning solution
Before purchasing a cleaning system, the following application analysis should be done on the cleaned parts: clarify the material composition, structure and quantity of the cleaned parts, analyze and clarify the dirt to be removed, these are to decide what cleaning method to use and judge the application Aqueous cleaning solutions are also a prerequisite for the use of solvents. The final cleaning process needs to be verified by cleaning experiments. Only in this way can a suitable cleaning system, a rationally designed cleaning process and a cleaning solution be provided. Considering the influence of the physical properties of the cleaning fluid on ultrasonic cleaning, the vapor pressure, surface tension, viscosity and density should be the most significant influencing factors. Temperature can affect these factors, so it also affects the efficiency of cavitation. Any cleaning system must use cleaning fluid.
When choosing a cleaning fluid, three factors should be considered:
1. Cleaning efficiency: When choosing the most effective cleaning solvent, be sure to do experiments. If ultrasound is introduced into the existing cleaning process, the solvent used generally does not need to be changed;
2. Simple operation: the liquid used should be safe and non-toxic, easy to operate and have a long service life;
3. Cost: The cheapest cleaning solvent is not necessarily the cheapest to use. In use, factors such as cleaning efficiency, safety, and the highest utilization rate of work pieces that can be cleaned by a certain amount of solvent must be considered. Of course, the cleaning solvent chosen must achieve cleaning results and be compatible with the work piece material being cleaned. Water is the most common cleaning solution, so systems using water-based solutions are easy to operate, low in cost, and widely used. However, for some materials and soils, etc., not suitable for aqueous solutions, there are many solvents available.
7. Different cleaning fluids, different cleaning systems
Aqueous system: Usually consists of an open tank in which the work piece is submerged. The complex system consists of multiple tanks and is equipped with a circulating filter system, a shower tank, a drying tank and other accessories.
Solvent system: Most of them are ultrasonic vapor-phase degreasing cleaning machines, often equipped with continuous waste liquid recovery devices. The ultrasonic vapor phase oil removal process is completed by an integrated multi-tank system formed by a solvent evaporation tank and an ultrasonic dip tank. Oil, grease, wax and other solvent-soluble soils are removed under the combined action of hot solvent vapor and ultrasonic agitation. After a series of cleaning processes, the unloaded workpiece is hot, clean and dry.
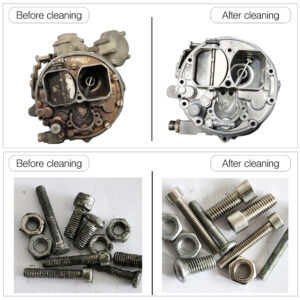
Before and after comparison
8.Cleaning parts processing
Another consideration for ultrasonic cleaning is the loading and unloading of the cleaning parts, or the design of the tooling in which the cleaning parts are placed. When the cleaning piece is in the ultrasonic cleaning tank, neither the cleaning piece nor the cleaning piece basket shall touch the bottom of the tank. The total cross-sectional area of the cleaning parts should not exceed 70% of the cross-sectional area of the ultrasonic tank. Rubber and non-rigid plastics absorb ultrasonic energy, so caution should be exercised when using these materials in tooling. Insulated cleaning parts should also be given special attention. Improperly designed tooling baskets, or holding workpieces that are too heavy, can greatly reduce the efficiency of even the best ultrasonic cleaning systems. Hooks, racks and beakers can be used to support cleaning pieces.
9.The cleaning time, work piece type, quantity is clear
※ Considering the use of machine working methods are fully automatic, semi-automatic and manual.
※Machine size and cost.
10. Other cleaning
Parts with a large amount of dirt are generally pre-cleaned by dipping, spraying, etc. After most of the dirt has been removed, ultrasonic cleaning of the remaining dirt works well. If cleaning small objects and objects (parts) with complex shapes, if a cleaning net is used or the cleaning object is rotated, and ultrasonic radiation is applied while vibrating, it can be uniformly cleaned. It seems that it takes a lot of work to choose a satisfactory ultrasonic cleaner.
Hello!