The Historical and Process of Ultrasonic Cleaning Technology
Browse Volume:1650 Classify:Support
Historical development
Ultrasonic cleanin g technology first appeared in the early 1930s. When the United States is located in New Jersey, the United States Radio Corporation in a laboratory of technical personnel. Try to use homemade rudimentary ultrasonic cleaning system to clean some objects, but the test was not successful.
On this basis, ultrasonic cleaning technology in the 1950s had a great development. When the use of ultrasonic operating frequency between 20 ~ 40 kHz. The range of ultrasound is use in thousands of different work situations. Many of which are other cleaning means can not work well in the occasion. Ultrasound can apply a very large amount of energy to the work piece. Especially for removing dirt firmly attached to the substrate. However, in some cases, the powerful energy of ultrasound can also damage the substrate material with dirt and fragile nature.
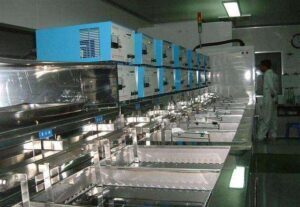
Industrial ultrasonic cleaner
Over the past decade or so, a number of technological innovations have emerged in the field of ultrasound. Which have improved the safety margin for removing contaminants from sensitive substrates. During this period, ultrasonic technology. Especially in the high frequency ultrasonic cleaning technology has a new development, and become the highlight of the industry.
In recent years, people found that the Granbosonic cleaning can remove from the surface of the semiconductor material ultra-fine dirt particles. And will not damage the surface of the substrate material. At present, this technology has been quickly popularized.
»(Granbosonic: According to the frequency of ultrasound. 40 kHz and below called conventional or low-frequency ultrasound. More than 1 000 kHz called high-frequency ultrasound. Also known as Granbosonic, referred to as Granbosonic)
Ultrasonic cleaning process
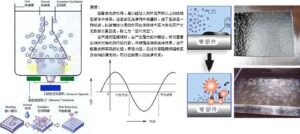
Ultrasonic cleaning process
Generally speaking, the cleaning process according to the object to be cleaned and the number of cleaning the degree of difficulty to decide. The main cleaning process is as follows:
1) Hot dip or spray washing: the purpose is to soften the work piece contaminants, separation, dissolution. And reduce the load of the next cleaning process.
2) Ultrasonic cleaning: the use of ultrasonic generated by the strong cavitation and vibration will be stripped off the surface of the work piece dirt, but also greasy dirt decomposition, emulsification.
3) Cold rinsing: the use of flowing clean water will have come off but still floating on the surface of the work piece dirt rinse clean.
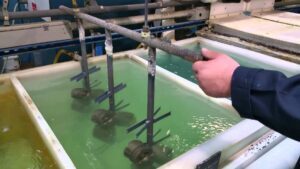
Industrial ultrasonic cleaner
4) Ultrasonic rinsing: solvent for clean water, the work piece immersed, the use of ultrasound will float in the work piece at the edges, corners and pores of the dirt clean.
5) Hot clean water and cold clean water rinsing: further remove the dirt particles hanging on the surface of the work piece.
6) Hot air drying: the use of a certain temperature and wind speed. So that the surface of the parts quickly dry.
Hello!